Gas Spring Pin Cushion Plate
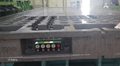
What do you do when the order specification for the sheet metal die calls for a cushion press and you currently only have a standard hydraulic or mechanical press? This was the scenario a die manufacturer in South Korea was facing before successfully securing a big order to Germany.
Facing a Substantial Investment
With assistance from the KALLER Korea team, the die manufacturer was successfully able to secure a big order of cushion pin dies.
The order destined for LÄPPLE GROUP in Germany was initially causing concern as the tool maker did not have the necessary press functionality to run and test the pin cushion tool properly. This is the pad and clamp force in a cushion die that is generated by air or hydraulic-driven cushion integrated and located inside or underneath the press.
Fortunately, with the aid of KALLER Korea, a ram cushion plate was designed, produced, and installed, saving the company from having to invest in a completely new press that would have cost thousands of dollars.
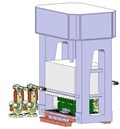
Requirements, Tooling Cost
A large quantity of different press cushions can be found on the market today, both air and hydraulic. A press cushion is a device located in or under a die block or bolster to provide all or additional pressure for stamping. Some can be pre-accelerated to reduce blank holder shock loading, and some can adjust the force applied to the blank holder throughout the press stroke.
Hydraulic cushions can apply the massive blank holder forces needed to stretch parts such as automotive hoods and door panels. Press cushions supply the force necessary to control metal flow by transferring the needed force through a cushion pin into the die.
A die manufacturer that is facing low-cost, low-production tools can rarely justify the high investment cost in an advanced system. For this reason, a less expensive standard press will often be used in low-production or prototype tool manufacturing.
Force Requirements
Simple conventional metal cutting dies, such as those used in blanking and piercing operations, often do not require a high-force system. In most cases, coil springs are sufficient. However, cutting operations such as fine blanking, may require forces a conventional coil spring cannot provide.
Also, metal forming operations, such as drawing, bending, and flagging, often require higher forces. The type of metal formed also affects the force requirements. High-strength material, such as those used in the automotive industry, usually requires higher holding and forming.
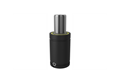
Global Differences in Use
The use of Gas Springs is almost standard in stamping die manufacturing as they have numerous advantages over conventional coil springs. They are available in many diameters, stroke lengths, and pressures. The KALLER global network of Gas Spring providers ensures quick deliveries and technical support.
Nitrogen Gas Springs can provide the force necessary to function as the force system for almost any stamping die application. Unlike Coil Springs, Gas Spring force can be regulated and controlled by changing the nitrogen gas pressure.
The nitrogen Gas Spring has many advantages: a high contact force without necessary preloading, a minimal total length, which allows the dies to be manufactured with a smaller shut height; and highly reliable. These long-life springs can achieve force unobtainable with Coil Springs.
Fewer springs can be used in the tool, and they can be piped together to create a system with uniform force. When piped, Gas Spring pressure can be monitored during production runs.
Although press cushions are widely used, the system is not common throughout all regions of the world. The South Korean market is one where a standard conventional press is preferred. This, from a tooling manufacturing perspective, acting on a global market sometimes can be a challenge.
Cushion Die vs Gas Spring Die
A cushion pin die operates using vertical protruding pins on the top or bottom. The pins have a corresponding contact point in the ram or bolster, which transfers the external force, pressure, or motion for stamping. This method of power transferal makes the pin die uniquely matched to the press and makes swapping the press line difficult.
The traditional Gas Spring stamping die is self-contained with the force located within the die itself. These dies can be mounted, if shut height and external footprint permits, to all common types of presses.
The Solutions
By adding an extra Gas Spring fitted plate as an adapter between the ram and pin die, with the same function as a cushion press, an existing press or press line can be upgraded.
At $75,000 – $100.000 USD, the cost of one Gas Spring Cushion Plate is far less than having to invest in a new press with cushion functionality, which usually is double that of a standard press.
Exploded view of a Gas Spring Cushion Plate with integrated, Gas Springs (left) and location in the press (right).
Living Up to Expectations
Working together with the customer, KALLER was successful in finding the solutions needed to overcome the current challenges.
By contacting your local KALLER representative, the likelihood of finding the best solution and product for your applicating increases. Go to kaller.com/en-us/contact to find your closest KALLER team.
Together we will secure your next project.
KALLER Newsletter
Want to stay up to date on all the latest KALLER news, including brand new case studies, as soon as they’re published? Sign up for our newsletter!