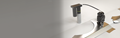
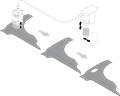
The market for Electric Vehicles (EVs) has grown exponentially since 2013 and is expected to continue growing at a fast rate. According to the International Energy Agency (IEA), the number of EVs in use in the world has grown from about 380,000 vehicles in 2013 to nearly ten times as much in 2017, with more than 3,000,000 EVs on the roads (see report).
The latest developments in the underlying technology and the attractiveness of government incentives, such as subsidies and exemptions from parking fees in some countries, add to the popularity of EVs. Several vehicle manufacturers are by now developing and releasing an offering of EVs and/or hybrids alongside combustion engine vehicle models to answer to market demand.
Simplify the Charge Port Cutting Process
An EV that is plugged into a power source to charge the batteries frequently requires an addition to the manufacturing process of the vehicle body. For vehicle manufacturers, this means that new requirements, in the form of fender variants for a vehicle body, need to be handled in the production process and the design of tools and dies.
For new vehicle models, manufacturers can set up the new production process to include an EV charge port for EV models but eliminate the port for other models – all in the same die. Using advanced, cost-effective cutting tools that can be positioned at a 360° angle and perform multiple operations in a die, a vehicle manufacturer can reduce the number of steps and tools required for producing a fender with or without an EV charge port.
Benefits of Using Advanced, Cost-Effective Cutting Tools
KALLER® Flex Cam simplifies cutting tools by increasing the number of operations in a die on a production line. The Flex Cam can perform high-precision, controlled piercing and stamping by using highly accurate guiding elements without side deflections.
Benefits Include:
- Simplifies process engineering, die design, and tool manufacturing.
- Enables positioning of KALLER Flex Cam at any angle, with 360° application area.
- Punches even upwards at negative angles.
- Adds operations and flexible solutions to new dies.
- Uses space efficiently.
- Reduces the total number of dies and tools with multi-functionality and durability.
- Protects against tool damage and over-pressure with controlled force and safety features.
Using KALLER Flex Cam Enables Vehicle Manufacturers To:
- Reduce production cost per part.
- Increase production rate and efficiency.
- Reduce tooling costs with fewer tool and die investments.
- Be more environmentally sustainable with fewer tools.
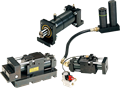
About KALLER Flex Cam
The KALLER Flex Cam has become a standard component for many vehicle manufacturers and is often included in different vehicle manufacturing tool standards globally.
The KALLER Flex Cam system has, with a proper set-up, performed more than 2,000,000 without any servicing required.
KALLER Flex Cam Solutions:
- Compact Cam CC 090-049
- Power Unit HCP 090-060
- Custom-made HCP Actuator, moved by an air cylinder or manually
For more information on the KALLER Flex Cam, please contact your distributor >>.
KALLER Newsletter
Want to stay up to date on all the latest KALLER news, including brand new case studies, as soon as they’re published? Sign up for our newsletter!